Quality Control
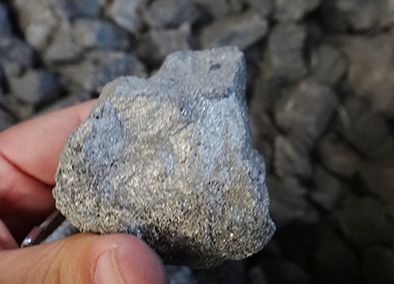
01. Raw Material Control
▪ Supplier selection: select qualified suppliers with good reputation.
Evaluate their quality management system, equipment and their traceability to raw materials.
▪ Factory inspection: conduct a comprehensive inspection before casting.
▪ Inspection record: record the incoming inspection results in detail.
▪ Inventory control: appropriate storage conditions and good inventory management.
▪ Raw material composition analysis: Inspect by spectral analysis and chemical titration.
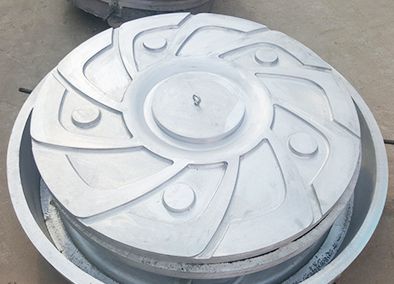
02. Mould Design and Manufacturing
▪ Accurate molds ensure the accuracy of the size and shape of parts
▪ Advanced mold manufacturing technology improves quality.
▪ Choose high-precision aluminum molds to optimize the production of alloy parts
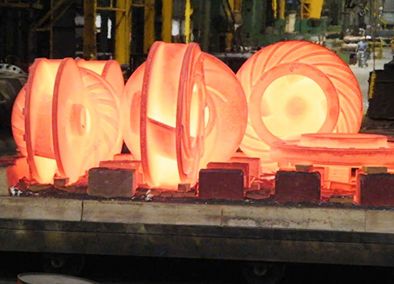
03. Quality Control of Casting Process
▪ Implement 5S management to improve shop floor efficiency
▪ Control of the moulding process to improve casting quality
▪ Improved quality control of the melting and pouring process
▪ The importance of cleaning, inspection and heat treatment in the casting process
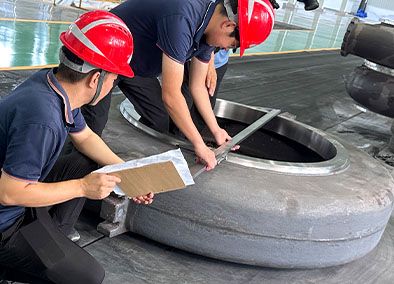
04. Machining Quality Control
▪ Adopting new high-precision CNC lathe equipment for comprehensive precision machining of spare parts, while strictly implementing the three inspection system for mechanical processing, is an important system to ensure product quality.
▪ Through three inspection stages, the quality and performance of machined products can be ensured to meet relevant quality standards and technical specifications.
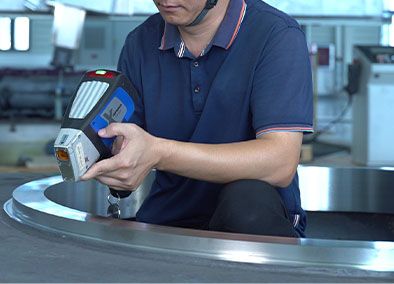
05. Quality Control of Finished Parts
▪ Assembly of bearing components: Select first-class brand bearings, check the inner diameter, outer diameter, width, parallelism of the two end faces of the raceway, and surface roughness of the bearings to ensure that there are no defects such as rust or spots. The rotation should be flexible and all contact surfaces should be cleaned properly.
▪ High quality accessory selection: 8.8 grade high-strength galvanized bolts and nuts, end cap, labyrinth sleeve, round nut.
▪ Experienced assembly engineers for strictly supervision
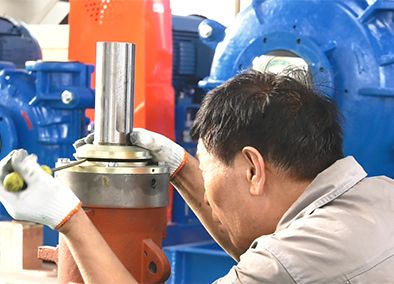
06. Assembly Quality Control
▪ Select first-class brand bearings, check the bearing's inner diameter, outer diameter, width, parallelism of the two end surfaces of the raceway and surface roughness to ensure that there are no defects such as corrosion or spots, and that they rotate flexibly and all contact surfaces are clean.
▪ 8.8 grade high-strength zinc-plated bolts and nuts, zinc-plated end caps, labyrinth sockets, round nuts, and other parts are strictly supervised by experienced assembly engineers.
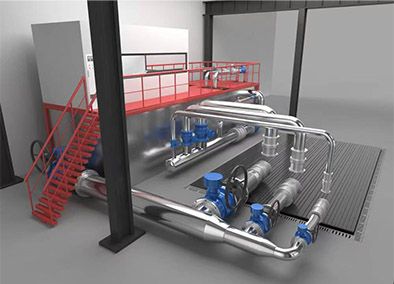
07. Performance Testing
▪ Energy performance testing: Including the relationship between head, efficiency, shaft power, and flow rate.
▪ Anti cavitation performance test: Mainly to determine the relationship between critical cavitation allowance and slurry pump flow rate, or to verify that the critical cavitation allowance of the pump is less than or equal to the required anti cavitation allowance specified.
▪ Noise and vibration performance testing.
▪ Bearing speed and temperature supervision.
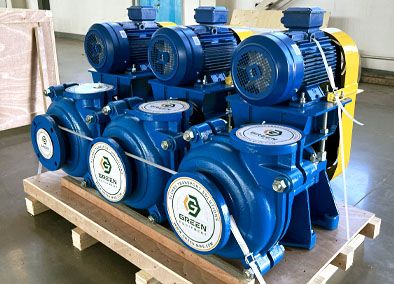
08. Packaging and Transportation
▪ Use sturdy packaging that meets export standards, with moisture-proof packaging film on the surface that can adapt to multiple handling and loading/unloading processes, ensuring that it remains intact during transportation and loading/unloading.
▪ All bulk components should be properly packaged, labeled with packaging labels, and the goods should be quickly and clearly identified and packed into suitable boxes.
▪ Use efficient and professional transportation agencies for transportation.

Click to unfold